Production Testing in Production Machines
- Precision Finishing Inc.
- Sep 22, 2019
- 4 min read
Updated: Nov 11, 2019
“Anyone can make a process work small scale and you can always produce stunning parts once. To achieve production level consistency, continually, with varying degrees of variables is where the challenge lies. We use the entire facility is a process development lab for that exact reason,” exclaims Jeffrey Bell, Technical Process Engineer at Precision Finishing Inc. “This facility was purpose-built for multiple finishing processes and the development of industry-focused chemical compounds and formulations.”
2017 Precision Finishing opened a brand new, state-of-the-art finishing facility, complete with Chemtrol® chemical production and laboratory. The building includes 16,000 sqft. of production area, with new and upgraded finishing equipment. The manufacturing area for the Chemtrol compounds product line consists of 10,000 sqft., with a warehousing/shipping area of 10,000 sqft.
Bell continues, “We are constantly testing finishes through many different processes like aggressive vibratory deburring to gentle polishing, non-abrasive blasting to high roughness substrates, shot-peened finishes, shot blasted finishes, industrial washing processes, centrifugal finishing and more, all while considering all pre and post-operational constraints.”
“Over the years, we have developed an extensive “finish library” for all types of diverse applications, from strictly function to beautiful aesthetics. We improve the surface of components to achieve all sorts of results like reduced wear, increased duty life, higher coating adherence, lower reflectivity, increased reflectivity, preparation for joining, reduction of processing times…the list goes on and on and on.”
Precision Finishing’s vibratory and blast media selections include over 50,000 lbs. and 100’s of part-numbers, encompassing many materials, shapes, sizes, and densities. For some processes, Chemtrol compounds are selected to aid in achieving a specific finish like brightening a surface, cleaning a specific oil, decreasing cycle time, protecting apart from impingement, encapsulating and carrying soils away.
In addition to constantly testing media and finishing compounds, the team will test different styles of pumps with varying flow rates, concentrations, and dosing methodologies. The testing process is rigorous and includes many iterations to compare against. Bell comments, “We routinely conduct R&D on pumps to ensure reliability, accuracy, and compound compatibility.”

The company works on 12-14 projects a month including:
● Industrial washing
● Waste treatment
● Standard vibratory finishing
● High energy vibratory finishing
● Wet blasting
● Dry Blasting
● Shot Blasting
● Accelerated Surface Finishing
● Shot Peening
The Chemtrol® line of chemistry is engineered and formulated for numerous mass finishing applications. From vibratory finishing, cleaning, heat treatment, corrosion control, and facility maintenance. “The formulation process looks at the many variables of the customer’s process and tries to come up with a cost-effective solution to their problem,” states Mark Slaska, Senior Lead Chemist at Precision Finishing Inc. “Cost-effectiveness is the main selling point, and it is a double edge sword trying to make the price-sensitive customer happy with a higher-performing formula.”
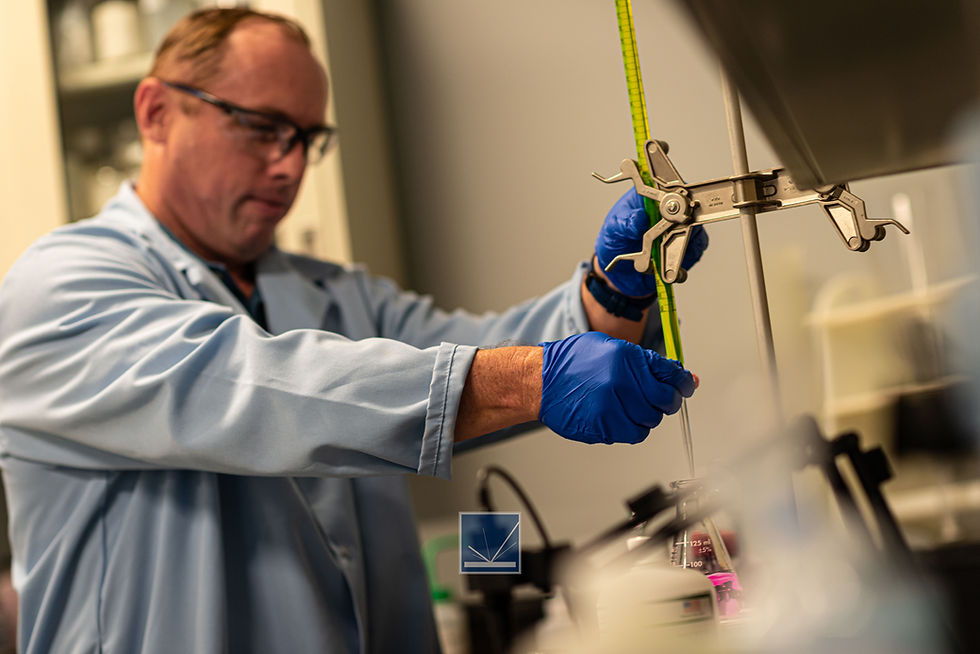
One of the variables is pairing the formulation with the processing equipment. Slaska explains, “The correct formula is critical to getting the surface finish for the customer. For example, the process could be a batch or a continuous flow. The compound choice would need to consider the cleaning power and the concentration, in-conjunction with foam level needed for cleaning vs. what can be tolerated. In addition to the time, pressure, concentration, and temperature constraints of the process, there is also the type of oil/soil that is being cleaned, the surface texture desired, and the waste treatment options needed on the backend.”
Manufacturing a high performing compound can be a difficult sell. “Many companies just look at acquisition costs not realizing that one half of a percent difference in concentration yields thousands of dollars in savings come year-end,” says Bell. Pairing a compound specifically to process or family of parts allows a smaller company such as Precision Finishing Inc. to provide a major benefit to companies looking to optimize their processes. Not only does Precision have a library of 150+ formulations but they can look at a specific oil or process constraint and formulate something specifically for that application, opening many more possibilities than companies offering a standard set of boilerplate chemistries.
To achieve the proper formula requires time and focus for development. The amount of time involved depends on the end goal of the formula and the process. Slaska elaborates, “A new formula can take a few weeks if it is a simple change or a few months if it is a new formula or difficult process. And of course, it can take years if a formula does not exist yet, for example, some of our accelerated chemistries or potential new ones.”
To keep track of all the formulations, Precision Finishing Inc. maintains a strict formulation quality program and “sample retain area” of all chemistry batches produced for a given time period. Each batch is recorded and preserved so formulation testing can take place if and process questions arise, so any variables relating to chemistry can be addressed.
From finishing processes to unique chemistry formulations, the company is in a continual research and development mode, helping provide complete finishing solutions that truly work for their customers.
Comments